For more than a decade, Georgia Department of Transportation (GDOT) has been focused on raising the bar on signal operations and maintenance. During this time, the Department has added more capability and the latest technology to remotely monitor signal performance. Referred to as SigOps, GDOT’s signal management approach leverages this technology to pinpoint issues faster and across more locations. As a result, SigOps has expanded the number of actively managed traffic signals in Metro Atlanta from approximately 1,800 to 4,000 using the same contract funding levels.
As part of a five-year contract, Gresham Smith supports GDOT and local government agencies in the Atlanta area with this cutting-edge traffic signal operations program. By helping GDOT implement its statewide vision for proactive signal management, our Transportation Systems Management and Operations (TSM&O) team helps the Department support additional signals, delivering greater benefits across the region and to the communities in the project area.
Commonly described by his peers as an elite “SEAL” member of the traffic signal technician community, Oliver Williams, a Senior Traffic Signal Technician with Gresham Smith’s TSM&O team, brings more than four decades of hands-on experience to the program. We recently sat down with Oliver to learn more about the SigOps program and dive into his remarkable career that includes a number of groundbreaking firsts.
Tell us about SigOps and how you play an important role in the program.
Oliver Williams: I think the first major thing to be aware of is the sheer scale that’s covered in our Western Region contract with GDOT for SigOps, which includes signals in Cobb, Clayton, Douglas and Fulton counties. There are more than 1,700 traffic signals within that project footprint, so it requires us to be very agile and nimble in how we go about supporting any issues that may arise.
Because of the large number of traffic signals we cover, GDOT has provided us with some really great tools that we refer to as GDOT’s signal toolbox, which helps us to remotely keep an eye on the performance of those signals and alerts us if they need attention. For example, it informs us of operational issues—critical ones—like an error in the signal controller where it’s no longer running its normal timing plan of green, yellow, red, and has gone into what we call “flash mode.” That means something urgently needs to be restored because the longer that signal is in flash mode, the greater potential there is for safety issues.
As a field technician, I have a boots-on-the-ground, eyes-on-the-street role that involves everything from troubleshooting, repair, and installation to preventative maintenance and other technical tasks. In other words, I make sure that everything is working the way it’s supposed to! I’m also in daily contact with our front-line stakeholders—the local government agencies that are also responsible for maintaining the signals—as well as construction-related staff who are managing projects that impact our signals.
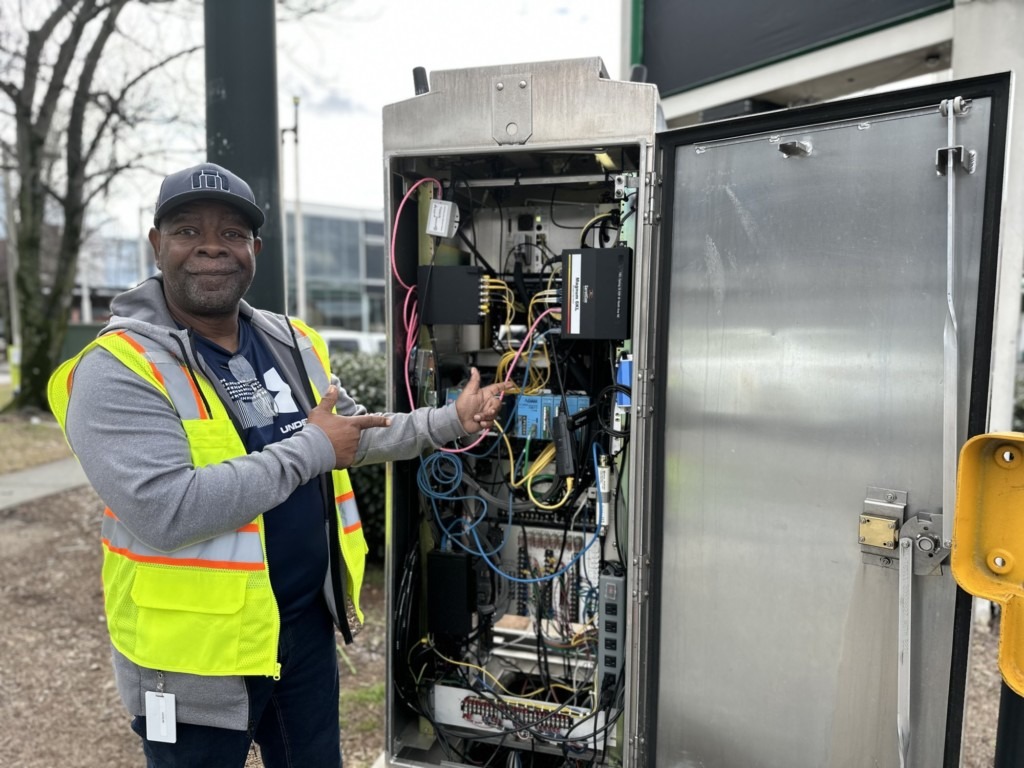
What is your favorite part of the job?
Oliver: There are so many aspects of the job that I love, like the problem-solving component to what I do; getting to the bottom of what’s going on with the equipment when there’s a problem. One of the things I really enjoy is working hand in hand with our engineers out in the field. We’re all working toward the same objective as part of an integrated team, which is to do whatever we can to get the most out of those signals that are key to moving people safely and efficiently through the Metro Atlanta region.
Were you introduced to engineering at an early age?
Oliver: Well, sort of. When I was about 7 years old, my family lived in a house with a large crawl space beneath where my dad would work on the electrical wiring to the house. Even though I had an older brother, my dad would always call me to come hold the flashlight while he was tinkering with the wiring, or he’d get me to hold a wire or flip a switch.
I asked my mom one day why he always asked me, and not my older brother, to help him. She said, “He sees something in you that he doesn’t see in your brother.” I didn’t understand it at the time, but I do now. I guess I always had a natural proclivity toward all things electrical. Looking back, my dad was always training me.
“Fortunately, I learned quickly and ended up becoming the first Black signal tech in Virginia.”
How did you get your start in the industry?
Oliver: I originally wanted to draw things, so I took industrial drafting classes in high school. When I graduated in 1978, I decided to take a job with the Virginia Department of Transportation (VDOT). I went into the position thinking that it involved drafting.
My first day on the job, I dressed for the office wearing a shirt, jacket, and a nice pair of double-knit pants. When I arrived, however, they put me in a van with a field crew and we drove out to a job site that was in the woods. When I got out of the van, I was handed a bush axe and told to cut a 150-foot path through some really thick brush. Turns out the position wasn’t for a draftsman—it was for a surveyor! As you can imagine, those double-knit pants were in pretty bad shape after I’d cleared that path.
I decided there and then that surveying wasn’t for me. So, I started taking electrician classes at night while I was surveying during the day. I was still working for the state when I applied for an electrician helper position they’d posted—and I got the job. It just so happened that the position was in the traffic-signal division, which I didn’t have a clue about.
I started out on a crew that traveled across the state installing traffic signals because contractors didn’t do that in those days. Fortunately, I learned quickly and ended up becoming the first Black signal tech in Virginia. About a year after that, I became the first Black person to obtain an IMSA (International Municipal Signal Association) Level I certification.
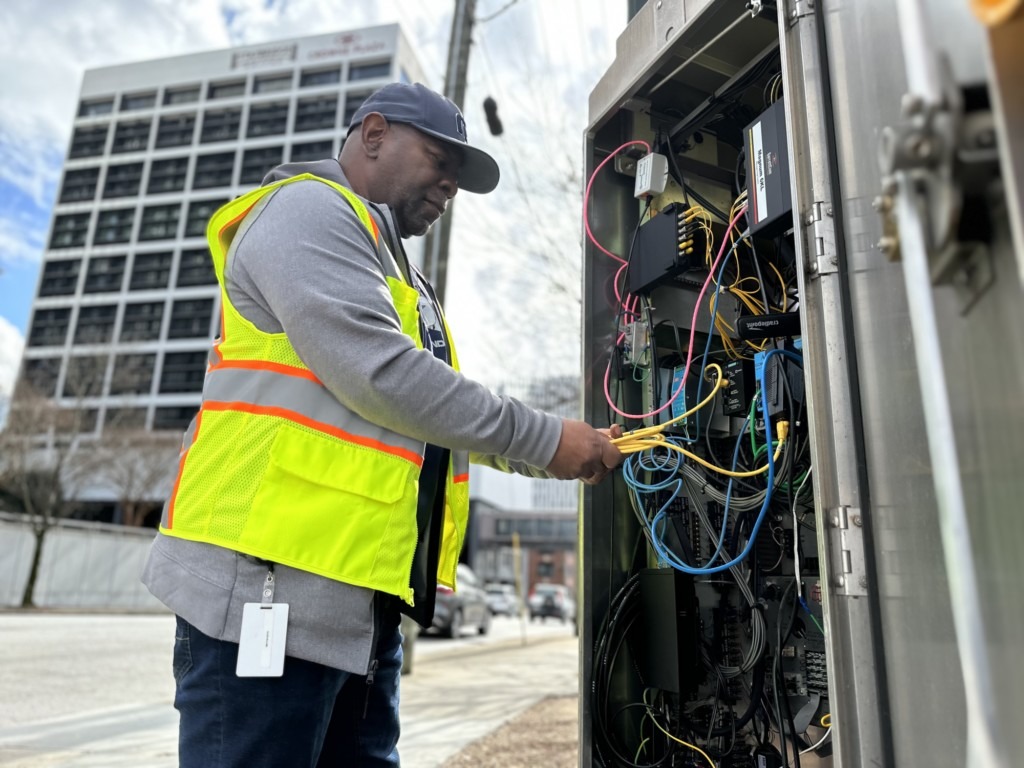
Why do you think you were the “first” in those cases?
Oliver: Because Black people simply weren’t exposed to those types of jobs at that time—you were almost always pushed in another direction. You’d rarely see a Black person in the role of an electrician back then, let alone working on traffic signals. And, unfortunately, that came down to racism as far as overlooking the promotion of Black people to certain positions; and a signal tech was one of them.
When I started in the traffic-signal Division, we had a crew of about 21 and there were only two Black people on the team—me and another guy, and he was the pole-truck operator, not an electrician. I remember thinking to myself: “Where are the Black guys?” Whenever we’d have a seminar, for example, there would only be one or two Black people out of maybe 300 people at the event. So, the opportunities simply weren’t there for us.
“I remember thinking to myself: ‘Where are the Black guys?’”
Why were you able to break through those barriers where others hadn’t?
Oliver: Honestly, I was probably very naïve. But when I wanted to know something, I became very outgoing, even though I’m not a particularly outgoing person in nature. I hadn’t been an electrician helper for long when a white supervisor became aware of my natural inquisitiveness and hunger to learn and he took me under his wing.
That’s where I learned about the inner workings of the signals, which was a game-changer for me. I remember him telling me that if I learned how to wire the cabinets, then I wouldn’t have to worry about another job in my life. And he was right. So, I kind of progressed from there, with many of the techs requesting me as their electrician helper.
I think one of the main reasons I was able to break through barriers is because I always wanted to know the why? and the how? and would stay past the end of my workday to ask the techs what they were doing and if they needed help. I learned so much that way, and I always wanted to be the best at whatever I was doing. When I was in the bucket working on the poles, I wanted to be the best bucket guy. When I was hanging the signal heads, I wanted to be the best signal-head guy.
How have things changed since you became the first Black signal tech in Virginia?
Oliver: I believe that things have changed for the better, or at least they’ve changed to an extent where if you want to become a Black signal tech, then you can go get it. When I first started in the industry, if you wanted it, then all you could hope was that someone would give you a chance.
Of course, there’s still some racial “stuff” that you’ll run into every now and then. But for the most part, we’re all brothers when it comes to doing what we need to do. When a traffic signal is down and there are two techs out there, we’re brothers and we have to figure out what’s gone wrong and how we can fix it.
Since those early days, you’ve continued to break through barriers in your field, including becoming the first Black engineer on the East Coast to obtain the IMSA Traffic Signal Level III Field Technician Certification. What’s next for Oliver Williams?
Oliver: I’m just excited to see what the future brings at this juncture of my career. I have a passion for sharing my knowledge with others, so I certainly want to continue to move the needle by training up the next workforce—and that includes helping out our local agency partners with training because, oftentimes, they don’t have enough of their own signal technicians due to a significant shortage in the industry.
I’m proud to say that a lot of the folks I’ve trained have gone on to do very well out there. Many of them have obtained their Level I and Level II IMSA certifications, and some have even gone on to make six figures. At the end of the day, I think it’s all about sharing what you know and taking a team approach. I think that’s one of the reasons our Western Region contract with GDOT is working so well. It’s the glue that binds us together in a really special way.